I was actually going to say that using this chart that I did ages ago and going from the rough 360+lbs.
I did find these.
Which came from this ebay link and they are coil over coils. The 7kg is around 400lbs roughly if my workings out are correct. The price is $120 plus $15 postage.
1 Like
Those spring would be about right, I would be worried about the ID being too small. I’ll do some searching to see if any other cars have the size and spring rate we are looking for. 
Before the latest trackday I had questioned what was next for Bertie and even wondering if I should sell him and look at a new project. Post trackday I have renewed interest and motivation to push forward and continue making Bertie better. I have set a deadline of about the this time next year as that’s when the next trackday I’ll be entering will be. Not all the things are track based, but, here is a list of things I’m hoping to achieve before next trackday I do:
-
new engine and gearbox mounts. The ones in there are 15-20years old. With the extra torque of the ej I think getting new mounts might be a good move
-
I still have an intermittent issue of a check engine light. I’m going to replace the o2 and coolant temp sensors in the hopes it’s one of those causing the issue.
-
L7 tachometer dash. The L9 Moves in Europe with the ej engines have this dash as stock. They use the same plugs as the L6 Move, so hopefully it’s just about re-pinning the plugs and good to go. We’ll see.
-
stiffer rear springs. As discussed above, there are a few options. I’m leaning towards the custom springs as I’m unsure if I have the tooling or skills to adapt the car or springs for coilover style springs.
-
lastly some bracing in the front. I know doing this most likely won’t add more grip, but, I hope it will make the car feel more stable and thus give me more confidence.
1 Like
well its funny you should say about bracing I messaged an ebay malaysion seller about a kenari front brace similar to what Jake gilbert has on his mira and yes they will post to australia. I will msg you the link when I find it again.
1 Like
I just messaged Curtis on the FB group who imports Ultra Racing bracing for the same brace (4 point strut) and a lower front brace too
. Our thinking it too alike.
2 more things I forgot to add to the list:
-
front lip and side skirts to reduce air getting under the car. Hoping this will reduce lift and also hopefully increase fuel economy on the highway.
-
long intake. Having a chat to @Mr_Gormsby on the track day gave me some insights into this. I remember reading on another thread how the length changed where is the rev range the increase torque would be. I wonder for everyday driving and track work weather the increase at 3500ish rpm or 2500ish would be more beneficial.
Where you want the torque depends on gearing. An ed or ef box is wide ratio. Needs to be pulling once a gear is selected more so than a bit of pull just before changing gear.
Your thought on lift and increased economy are separate things. Unless you can run a good computer model I will guarantee an improvement in one of those areas will be at the cost of the other. Adding more down force on a production sedan is going to cause significant drag. Reducing drag is not going to have an effect on down force. There was a thread on ecomodder about an aero L200. Just looked it up now and the pics seem gone.
. Aero forces increases with the square of the speed, you will find any effects of pushing through the wind at 50kph is four times as great at 100kph. I am going to suggest that a focus on reduced drag is going to be more important than that of downforce. Downforce is something to focus on when you are at the limits of corner traction, or perhaps something needed if high speed stability is an issue. Big aero often needs big power to push the wind.
For us air going under the car is where engine heat goes. Even with a skirt going completely to the ground air flow under the car can’t be stopped. One works to create a pressure differential and a “suction” benefit that can be great than that of placing wings on any vehicle. It is how that air is directed. One wants a low pressure. Rather than a poor explanation on my part check out https://www.verus-engineering.com/ . Not sure it is their website of facebook page, but they share a lot of analysis and explain what they have found to happen with small changes of skirts, clean under body, wings and diffusers.
On bracing I could be wrong, but I think most are useless and just add weight (esp the strut brace and under guard ones). From my experience the first place to start is solid mounting the K frame will provide more stiffening than any “bolt on”. The next brace needed is one on the K frame and should go between the lower control arm pick up points. I think these bolt on things have a mostly placebo effect and are popular because they are easy to bolt on and then you can say “hey I did a thing”. The L200 needs something to help diagonal flex oh the shell. The simplest way is to measure the door gaps at the top rear most corner of the door with the car on flat ground. Mark the spot on the door and the adjacent point on the B pillar. Jack the car and put it down so the full weight is on the LHR and RHF. Remeasure. Then LHF and RHR. Remeasure. If you get a mm or two diff that is where all you chassis problem is. I do the diagonal measure another way. A little flex like that in a static situation is multiplied many times in a dynamic situation. Suffice to say during my local hillclimb test track runs my interior light did at one stage begin flickering in corners and the door rattling. Hmm, didn’t do that before, but I am pulling more revs out of that bend than before, so I am going faster than the last time. The next stage of modifications brought more corner speed again. On the climb though I began running out of travel (need more front rate) and hitting the bump stops when at full attack. It was at this point the doors started opening due to so much flex. Most worthwhile bracing needs to work in three planes and not just one or two. They need cross chassis bracing or diagonals .I am certain the money is better spent elsewhere than the off the shelf bracing, especially money spent on strut inserts (Koni Red as a min), rear shocks/dampers (Spax adjustable and then Koni as a min) and springs. Then buy the best tires you can.
2 Likes
Thanks MrG. I wonder with the longer intake how quickly the torque curve tapers off?
The Lower control arm brace is one of the ones I want, so I’m glad it is one that might actually help
. I’ll probably still try a 4 point front strut brace like this one. I’ll see how it feels. In regards to solid mounting the K frame, is that a case of removing the rubber mounts and replacing them with something stiffer or just removing them?
Regarding the front lip/airdam using the link you supplied I found this article. From their testing lowering the car and adding a front dam/lip both deceased the drag coefficient and increased downforce (going from lift to downforce). Since I do most of my travelling on the highway the better drag coefficient would hopefully equal better fuel economy and the increase in downforce should make the car more stable at these speeds. Any reduction in the amount of air that currently goes through the messy front suspension (you can easily see the sway bar under the bumper) of a Move the better. Of course the Move is no MX-5 and I’m not driving at 100m/h, so maybe the results should be taken with a grain of salt. But, without a wind tunnel or modelling that I can easily access my best resource is to try it for a week and see if I feel it adds stability on the highway (I’m sure adding a lip did for my sirion) and see what it does.
In my case the torque curve does not seem to taper off. The trade off is less throttle response and some power loss perhaps 1%. Power is a function of torque and time. That the air has to travel further means potential maximum power could be down. But power is often up lower down in the rev range enough to offset the loss higher up. Drag racing needs big power, track work needs torque to get out of corners quickly. The only drag race is on the main straight at QR but there are seven corners you have to get out of in a hurry.
In my view, based on my formal engineering study and experience, the four point brace will be a hindrance and can have no benefit whatsoever. However, test it yourself. But a blind test would be best. You should drive it with and without, having no knowledge of whether it is on or not (yes someone else would have to fit it). The top point is so far away from the K frame front mount that I can’t see what it would do. This sort of thing would be the direction I would take,
though it is still not right since the strut top brackets pick up the triangulation well to far inboard. The triangulation is right and picking up in the center of the firewall “will” work.
Removing the K frame rubber was not my first step. Instead I cut them down to just a cone shape and shortened the crush tube. Something needs to remain to allow the frame to be centered on the the chassis studs. But the rubber is shortened enough that the metal of the K frame touches the chassis. The step after than is to make delrin or alu cones to center all. What I did was weld up the K frame holes to a std smaller diameter and then machined up something rigid to locate the frame on the pins (can’t remember if that was steel, alu or delrin - I’d have to look under the car or see if I have shown this in my thread). Anyway this stops the K frame from floating on the chassis. Raising this means adjusting the steering coupler that goes to the rack. If a car is lowered raising the K frame corrects the roll center.
Concerning the Verus article, you are spot on. Doing something with as much informed knowledge is how I start off. By using what they learnt you are not just going on what looks good (I must say those with understanding do end up knowing by “looks” if something will work, but that is not “it looks cool”). You can do a bit of testing with wool tufts http://www.autospeed.com/cms/article.html?&title=Aero-Testing-Part-1&A=108656 I’ve meant to do this many times but other than putting one or two tufts on the bonnet I am yet to make a serious effort, but still want to. I am building a small race car at work that needs to have super low drag and it will be the perfect thing to do this with (only 30hp and will have a tops speed of 80kmh https://www.facebook.com/Formula-High-School-Formula-Student-RTO-Code-41124-1391695151087468/) . I have looked for low pressure areas using a diy manometer or a Magnehelic gauge of which I have two that cover a range of pressures and one which is low resolution across a narrow range. These manometers are excellent for seeing if you end up with high pressure under the car. My use is more for looking for where to place an air intake, since you should not put an intake in a low pressure area nor hot area. Find a high pressure spot and that is where the filter inlet should go if there is space. This is a fantastic discussion and would be a huge contribution to the community to see some data. A Move - stable (kind of a contradiction in my mind) and speed (no association in my mind) - the perfect challenge and I do love the irony of your success so far achieved by all of you Move guys!
1 Like
I am absolutely loving this discussion and am reading everything and looking at links intently. My move has an Lca Brace underneath it and I do feel it helps, but unfortunately I have nothing to really compare it with as when my move did not have it on it was a very slow auto and I did not see the point of it until I went 4x100 and installed at that time.
In driving styles between Rob Hovey and I at QR I think he is a much more capable driver (more adapted or natural) than I. He definitely catches on quicker than I do and that shows by his time slip being 1 second behind in one of the rounds where I am much quicker on straight and I had semi slicks on and an Lca Brace and also a jackshaft.
Rob was still able to throw his move around corner’s in a more aggressive way than I could until the later rounds. I am not sure the jack shaft did do a lot of help as lets face it a live axle is a live axle and no lsd.
With areo qould it be and idea if not a splitter then would it be an idea to have say an under car guard that stops any wind flow within the underparts of the engine and block airflow though as much as possible through the front of the car with the exception of the radiator? My car is flawed for this as I have the big bonnet scoop for the intercooler and the air flow does get trapped in there also as it in not exactly efficient. What I have noticed with it though is the air flow that does come through now pushes down through the back of the engine bay and under the car and this can be felt by how much heat is now generated towards the foot area and tunnel area of the car while driving. If I went for front mount intercooler in future I think I would look more into the aerodynamics flow to be maximised.
In all I think for us move guys on track the fun is making something that has no place on a race track as competitive as we can and still hilarious at the same time. I must say at the end of round 2 last sunday If I wasn’t smiling you could’t wipe the smile off from the inside. To make it to go back out on track and keep going was just the best feeling ever and just so much fun!
2 Likes
Race a Move is such a great contradiction of their purpose. Very interesting and loving the problem solving.
2 Likes
I love that we can have these discussions. It’s what makes this forum worth having.
Thanks for you comments regarding my driving. The reason I wrote up above that I’m just the stupider driver is that I realised after the first trackday that one of the major limiting factors for my lap times wasn’t the car, it was my own head. Since that first time at Lakeside I’ve been lucky enough, through work, to go go-karting a few times and have worked on ignoring the self-preservation part of my brain to push harder. Thus ignoring all the smart things I should do, be a bit stupider and push harder. To me that battle in my own head is half the fun of being on track. Knowing I should be braking or slowing down, but, fighting the urge even just for a second in the hopes of a better time. Love it! I scare the shit out of myself each time though 
This is why I said above that even if the bracing does nothing but increase my confidence in the car it would probably still make me faster.
A undertray that smooths out any part of the under body, especially at the front under the engine, would be of benefit to speed up airflow and minimise turbulence under the car. The mx-5 guys do something like this:
and the crazy rx7 bois are doing things like this:
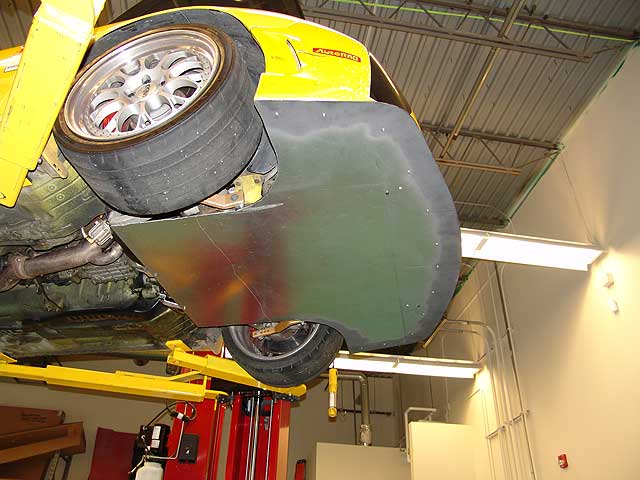
A rear defuser would also be of help. However, for me at least, wouldn’t be doable unless I get a new exhaust system. I wonder how much of a benefit these would have?
2 Likes
Concerning driving. One needs to know or be able to predict what the car will do. Inputs are done to put a car where you want it before it gets there. For example, in a slide I don’t want to be correcting such as an unexpected event but rather know that what I’ve done is going to make it slide (did a bit of intended power oversteer only on the happy laps by having the car unsettled and then the relatively little power helped hold the line). Another example is turn two where I can gauge on entry just where the car will end up on the exit when the apex is hit right. A lot of my modulation to correct unexpected outcomes is left foot braking, though I intend to left foot brake amid traffic in three through six at QR knowing prior to entry when I can’t take the fastest line and will want a tight radius. The point is that nothing that happens should be unexpected, and that includes getting that tires might be different on lap five to lap one, and same with brakes and so on.
The undertray nearly always works but there are okay solutions and excellent solutions. Angle is important and it should not start behind the leading edge but at or in front of the leading edge. My removal of the tire well was in consideration of better exhaust path, weight reduction and for a diffuser. This latter item must have vertical strakes on the outer edge and the diffuser angle is critical.
1 Like
Its funny you say about the cornering especially at turn 2. Last year in the wet and with street tyres I worked out how to take that turn and use the slide to my advantage. This year with semi slicks and dry there was no slide at all and all grip. I had to use the track differently going in and coming out and really make use of getting close to the apex and having to run nearly on the ripple strip coming out. It really wasn’t until rounds 3 and 4 I was staring to feel my footing. Turn 4 was a front inner wheel lift and spin by then but it was the best way to take that turn I found. I would try to go that little bit wider and try to stop it for more grip but couldn’t quite get it.
1 Like
Front wheel must never ever lift as you loose drive. Soft front and stiff rear
1 Like
Yes going the softer king spring in frond and will get stiffer rear.
1 Like
Being able to predict how the car will act or the line that it will take, requires a familiarity with both the car and track days that I am at this stage lacking in. Though I’ve had this car for over a year I have only driven it for about 5 months of that and at speed only on the track. I feel still quite the novice when it comes to driving on track. As I settle with the car and become more comfortable with driving it at 10/10ths I hope to be able do better. I must admit that this time on track I was definitely driving by instincts and not thinking about best lines and such. If I was on track by myself I would probably focus on cornering lines more.
I had traction issues exiting turn 4 as well. I remembering it being quite bumpy and felt that was the contributing factor in not being able to get power down.
2 Likes
Yes, knowing the track is really important. I am sure if I’d gone out this weekend for a redo I’d be half a second quicker at least. Plus the format was unfamiliar. I normal tinker with set up by only checked tire pressure once. Needed to bring all pressures down from 30psi to 24psi and would have gained a tenth or two. All my comp does help, however, motokana is mostly first gear and some reverse, Khanacross is moslty second gear and a bit of third and hillclimb is a different animal with lower speeds but much much more dangerous or unforgiving of mistakes. So knowing what is going to happen in higher than “on the road” speed is not something we get much prac in.
I had little drive/traction issues as the ol’ wagon puts the power down well. Hoping to go to a computer controlled DCCD gearbox with front LSD. I plan to get that in next Saturday morning (Qld Hillclimb champs at Mt Cotton both days so I hope to get out for each day, esp all Sunday as part of a pit crew). The new box will help a lot in Khanacross. My next event is sixth or seventh of Juen and I hear the WRX club will be there. Hoping for my normal top five outright finish with them there - car setup, having to remember the course and my experience should hold me in good stead. Wanna do a khanacross?
1 Like
I am still waiting on a quote regarding the custom springs from King Springs (had to request quote through Repco), but, I did get a response from Lovell Springs. They quoted $440+shipping for a pair.
2 Likes
Quick update on some of the things I’m working on before next trackday:
In regards to the rear springs; I spoke to a suspension shop on the recommendation of MrG and the bloke there suggested the best option would be modifying the rear to take coilover springs. This would widen the range of springs available and mean we could fine tune spring rates by 50lb/in increments.
Next, regarding in intake setup. I was talking with my soon to be Brother-in-Law(henceforth known at the BiL) regarding having a bellmouth/velocity stack/ Venturi at the start of the intake, possibly in the filter itself. The BiL is an engineer, has offered to 3d print a bell mouth in a heat resistant abs plastic with the proper venturi curve. I would just need to provide him with what I want the OD for inlet, ID for outlet and length required. I think ID for outlet would be 40mm and OD of inlet would be based on what filter I get, so, I guess I need to figure out what filter would be used. Any suggestions on a filter?
2 Likes
Have a look at my thread to see where the filter sits. I use a K and N pod type. It has an opening big enough to go over the bell mount and clearance on the inside, back side and front side. The gap is filled with a C shape bit of plastic that when closed into an O has the right ID and OD for a band clamp to go over the filter and clamp the C to the ram pipe (I may have used some foam as gasket inside all). My pipe is all 40mm pvc pipe wrapped with silver sisalation tape and using 40mm silicone bends. I did the maths at one stage and 40mm was pretty close to my revs and power expectation.